The Scientific Research Behind Porosity: A Comprehensive Overview for Welders and Fabricators
Recognizing the detailed devices behind porosity in welding is crucial for welders and makers aiming for remarkable workmanship. From the make-up of the base products to the complexities of the welding process itself, a plethora of variables conspire to either worsen or minimize the presence of porosity.
Recognizing Porosity in Welding
FIRST SENTENCE:
Assessment of porosity in welding reveals critical insights right into the integrity and high quality of the weld joint. Porosity, identified by the existence of dental caries or voids within the weld steel, is an usual issue in welding procedures. These voids, if not effectively addressed, can endanger the structural stability and mechanical residential or commercial properties of the weld, bring about potential failings in the ended up product.
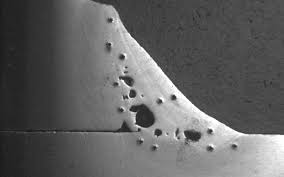
To detect and measure porosity, non-destructive testing approaches such as ultrasonic testing or X-ray inspection are commonly utilized. These strategies allow for the identification of internal problems without jeopardizing the stability of the weld. By examining the dimension, shape, and distribution of porosity within a weld, welders can make enlightened choices to boost their welding procedures and attain sounder weld joints.
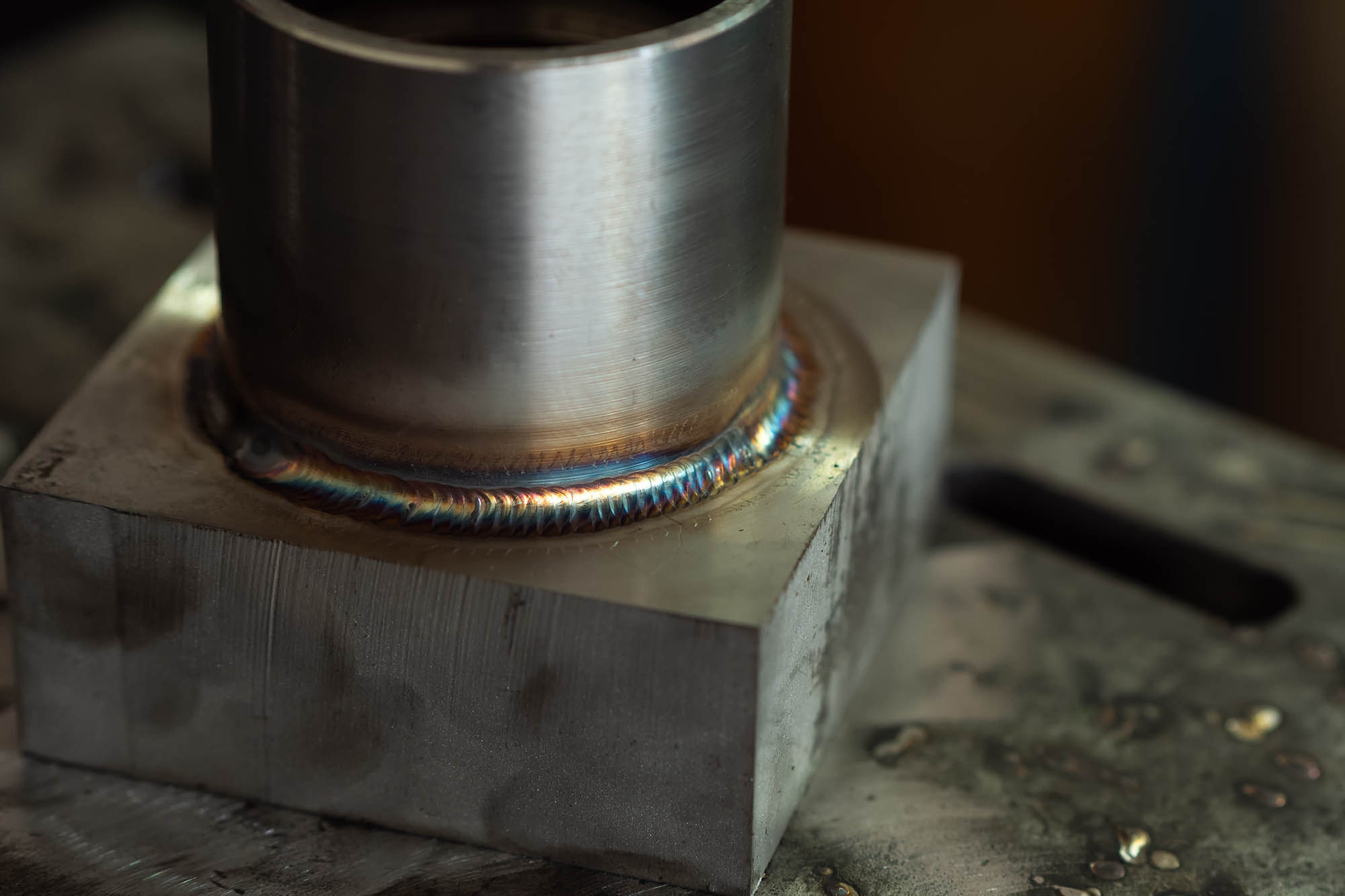
Aspects Affecting Porosity Development
The incident of porosity in welding is affected by a myriad of aspects, ranging from gas securing effectiveness to the details of welding specification setups. Welding specifications, consisting of voltage, present, take a trip speed, and electrode kind, also influence porosity formation. The welding method employed, such as gas metal arc welding (GMAW) or secured metal arc welding (SMAW), can affect porosity development due to variations in warmth distribution and gas protection - What is Porosity.
Results of Porosity on Weld High Quality
Porosity development considerably endangers the structural integrity and mechanical residential or commercial properties of bonded joints. When porosity is present in a weld, it produces gaps or cavities within the material, lowering the overall stamina of the joint. These gaps act as tension concentration points, making the weld more susceptible to splitting and failure under tons. The existence of porosity additionally compromises the weld's resistance to deterioration, as the entraped air or gases within deep spaces can react with the surrounding atmosphere, leading to degradation gradually. Additionally, porosity can hinder the weld's capability to hold up against stress or influence, more threatening the general high quality and reliability of the bonded framework. In important Bonuses applications such as aerospace, automotive, or structural buildings, where safety and security and durability are paramount, the detrimental results of porosity on weld top quality can have extreme repercussions, stressing the importance of lessening porosity with correct welding techniques and treatments.
Techniques to Minimize Porosity
To boost the high quality go to these guys of bonded joints and guarantee structural stability, welders and fabricators use details techniques intended at decreasing the development of spaces and tooth cavities within the product during the welding procedure. One effective method to decrease porosity is to guarantee proper product preparation. This includes comprehensive cleansing of the base metal to eliminate any type of impurities such as oil, grease, or moisture that could add to porosity formation. Additionally, using the proper welding criteria, such as the correct voltage, existing, and take a trip speed, is vital in stopping porosity. Keeping a constant arc size and angle throughout welding also helps reduce the probability of porosity.

In addition, picking the appropriate securing gas and keeping correct gas circulation prices are essential in lessening porosity. Utilizing the proper welding method, such as back-stepping or utilizing a weaving motion, can additionally help distribute heat evenly and reduce the chances of porosity formation. Making sure appropriate ventilation in the welding environment to get rid of any kind of possible resources of contamination is important for achieving Visit This Link porosity-free welds. By implementing these techniques, welders can effectively minimize porosity and generate high-grade bonded joints.

Advanced Solutions for Porosity Control
Executing sophisticated technologies and ingenious approaches plays a critical duty in achieving remarkable control over porosity in welding procedures. Furthermore, using advanced welding strategies such as pulsed MIG welding or modified environment welding can also assist minimize porosity issues.
One more innovative option involves using sophisticated welding equipment. As an example, making use of equipment with built-in functions like waveform control and advanced power resources can enhance weld high quality and minimize porosity risks. The execution of automated welding systems with precise control over specifications can substantially decrease porosity flaws.
In addition, including advanced monitoring and evaluation innovations such as real-time X-ray imaging or automated ultrasonic testing can help in finding porosity early in the welding procedure, enabling for instant restorative actions. Overall, integrating these innovative remedies can substantially boost porosity control and improve the general quality of welded parts.
Verdict
In conclusion, recognizing the science behind porosity in welding is essential for welders and makers to produce high-grade welds - What is Porosity. Advanced options for porosity control can further improve the welding process and make certain a solid and dependable weld.